In stainless steel production, uninterrupted uptime isn’t just a target; it’s critical. From powering automation and actuators to supporting cooling and descaling systems, compressed air plays a crucial role in ensuring every part of the mill operates at peak performance.
Facing increasing production demands and a harsh, dust-heavy environment, a leading European stainless steel producer realized its compressed air system was holding it back. While their FS-Elliott P700 centrifugal compressor had delivered reliable service for over 13 years, the fleet of five rotary screw compressors had become a maintenance and energy drain.
Future-Ready Compressed Air: A Strategy for Growth and Reliability
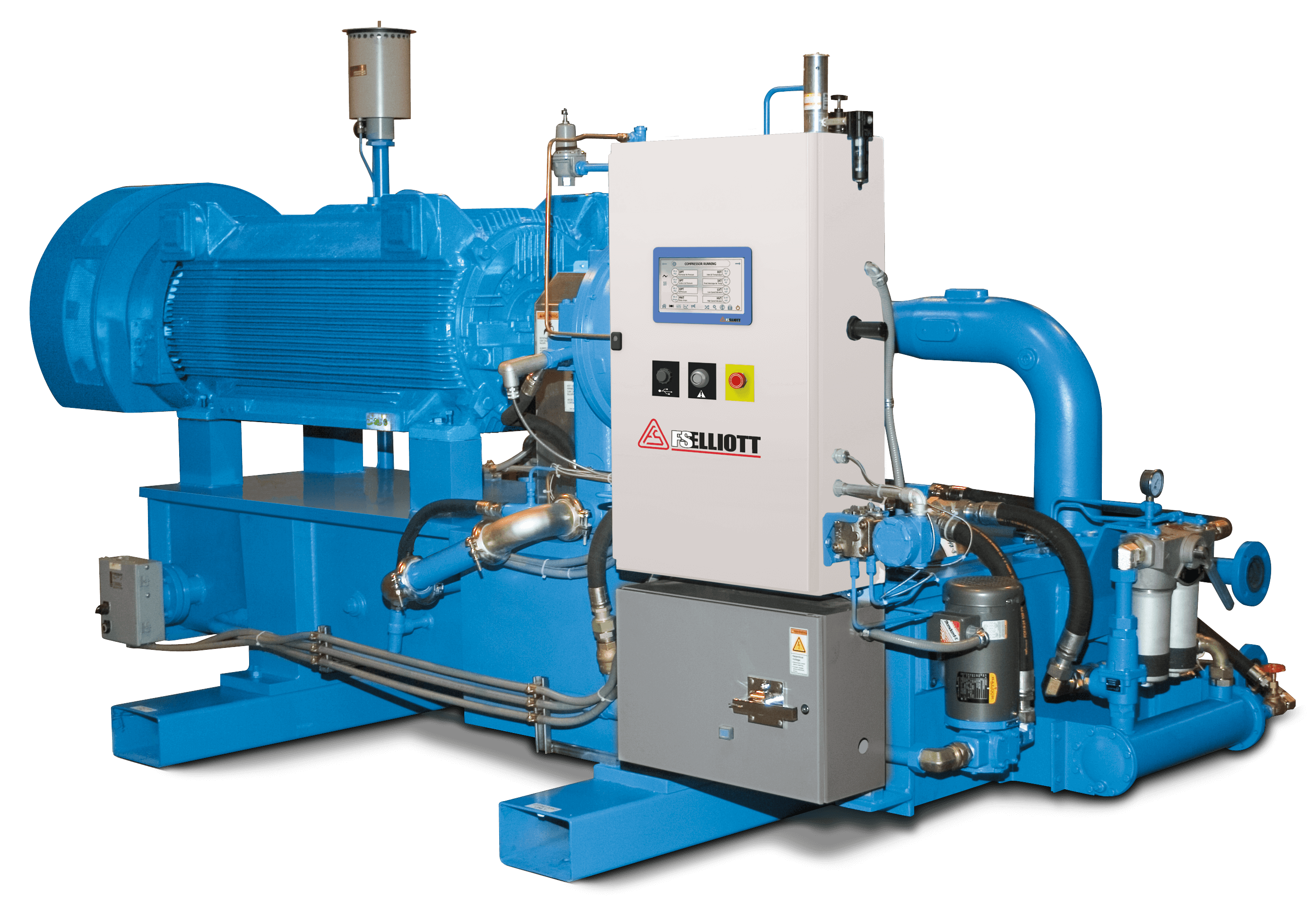
Recognizing the risks of unplanned downtime, including lost production, scrap, and higher energy costs, the facility’s engineering team partnered with FS-Elliott to create a robust, future-focused solution. Together, they set two strategic priorities:
- Modernize the existing P700 compressor by integrating advanced controls and protective measures to enhance efficiency and extend operational life.
- Install a new P400 centrifugal compressor, allowing the plant to retire five aging screw compressors, reduce maintenance costs, and improve system reliability.
Tailored Engineering for Demanding Steel Operations
The project included a comprehensive field overhaul of the P700, utilizing FS-Elliott’s removable airend design to minimize downtime. The integration of the R1000 control panel enhanced both energy performance and monitoring capabilities. Meanwhile, the newly installed P400 unit was designed with a remote-mounted inlet air filter to ensure cleaner air intake and featured custom aerodynamic components to handle the high-temperature, high-pressure demands of steel production.
Measurable Savings & Sustainable Impact
The impact was immediate and measurable. The plant reduced its energy consumption from 0.1125 kWh/m³ to 0.104 kWh/m³, generating annual energy savings of approximately $40,000. Beyond operational improvements, these upgrades enabled the facility to qualify for substantial energy grants through European Community funding.
A New Standard for Sustainable Steel Production
This transformation showcases what’s possible when advanced centrifugal technology is combined with expert collaboration. By modernizing its compressed air system, the facility not only increased production capacity and reliability but also set a new benchmark for energy efficiency and sustainability within the steel industry.
Explore the Full Story